Common Steam Boiler Issues and How to Fix Them
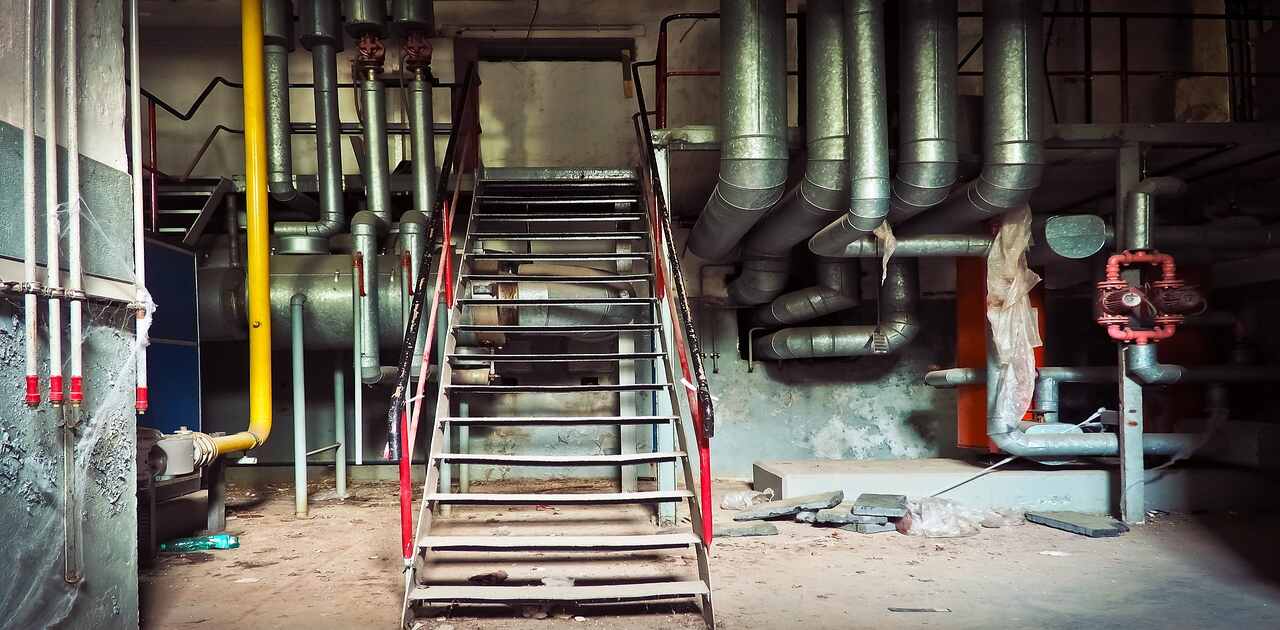
Troubleshooting is an important aspect of keeping steam boiler systems in excellent working order. Many industrial and commercial activities rely on these complex systems for a consistent source of heat and energy. However, because steam boilers are complicated and must cope with a wide range of practical obstacles, problems might occur that impair their performance.
Troubleshooting is vital in these scenarios because it allows engineers and technicians to rapidly and easily locate, diagnose, and correct problems. Professionals can use methodical processes and their knowledge to ensure that steam boiler systems work smoothly, increase safety, maximise efficiency, and minimise downtime. As a result, knowing how to repair steam boiler systems is critical if you want to keep operations operating smoothly and protect the overall productivity of numerous sectors.
The purpose of this article is to provide a comprehensive overview of the most prevalent boiler system issues and practical solutions. There are numerous things that can go wrong with steam boilers, affecting their performance, economy, and lifespan. Changes in pressure and water level, as well as scaling and corrosion, can all make it difficult for boiler systems to function properly, lowering productivity and increasing operating expenses.
Recognising the importance of resolving these issues as soon as possible, this section goes into detail about each typical issue, outlining what causes it and what impacts it has. It also provides practical ideas and procedures for diagnosing and resolving issues that have been discovered. This provides specialists in the field with the information and resources they need to maintain boiler systems working efficiently and for a longer period of time.
This article aims to provide industry professionals with the knowledge they need to ensure that steam boiler systems operate consistently and efficiently. It accomplishes this by discussing common boiler problems and providing effective remedies.
Understanding Common Steam Boiler Issues
Problems may impair the performance and efficiency of a steam boiler. When the boiler fails to generate enough heat or convey it to the designated medium, poor heat transfer ensues. Heat transfer from combustion to water or steam can be hampered by scaling or deposits on heat transfer surfaces. Corrosion causes structural damage and lowers efficiency.
Corrosion can be caused by water treatment, oxygen penetration, and acidic condensate. Issues with pressure, water level, and combustion efficiency can all have an impact on boiler performance and safety. Understanding these common problems allows steam boiler systems to work more smoothly and last longer.
Inadequate heat transmission is indicated by insufficient steam generation, thermal efficiency, or uneven heating over heat transfer surfaces. Heat transfer and contact area can be reduced by scaling and deposits on heat exchanger surfaces.
Corrosion is indicated by pitting, rust, and boiler system leakage. Inadequate water treatment, excessive feed water dissolved oxygen, or combustion byproduct acidic condensate can all cause corrosion. Failures in the pressure regulator or control system might result in fluctuating pressure levels or safety valve discharges.
Inconsistent water level readings caused by faulty level sensors, improper blowdown, or water carryover indicate a problem with water level control. Finally, irregular flame patterns, a significant amount of unburned fuel, and excessive smoke emissions indicate problems with combustion efficiency.
These issues could be caused by air-to-fuel ratios, burner maintenance, or fuel quality. By identifying symptoms and causes, professionals can diagnose and repair steam boiler problems.
Low Water Level and Water Pressure Problems
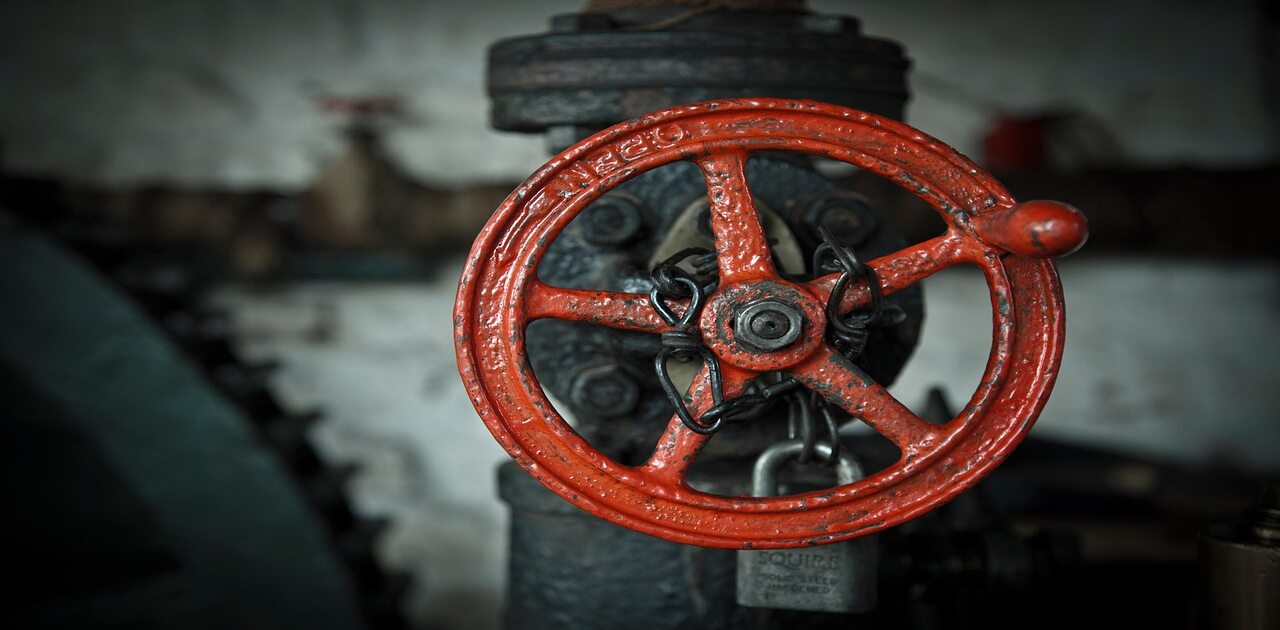
Causes and Symptoms of Low Water Level in Steam Boilers
Causes of low water level in steam boilers can include:
- Insufficient water supply due to issues with the feedwater system or valves.
- Malfunctioning water level controls, including faulty level sensors or control switches.
- Improper blowdown practises lead to excessive water loss.
Symptoms of low water level in steam boilers may include:
- Unusual noises from the boiler, such as banging or rattling.
- Inconsistent or low steam production.
- Safety valve discharges or pressure fluctuations.
- Boiler shutdown or tripping due to low water cutoff devices.
- Visible indications of dry or overheated heating surfaces.
Solutions for Maintaining Proper Water Level and Pressure
- Checking and adjusting water level controls:
- Regularly inspect and calibrate water level controls, ensuring they are functioning correctly.
- Verify that level sensors are clean, properly installed, and free from any obstructions.
- Adjust control switches or settings to maintain the desired water level within the boiler.
- Addressing leaks and ensuring proper water supply:
- Conduct thorough inspections to identify and repair any leaks within the boiler system promptly.
- Inspect and maintain the feedwater system, including pumps, valves, and pipelines, to ensure proper water supply.
- Test and verify the functionality of automatic water makeup systems to prevent water shortages.
- Implement proper blowdown procedures to control water impurities without excessive water loss.
- Regularly monitor and maintain the water treatment system to prevent scaling or corrosion, which can lead to low water levels.
By implementing these solutions, steam boiler operators can effectively address low water level and water pressure problems, ensuring the safe and efficient operation of their systems.
Poor Steam Quality and Distribution
Signs of Poor Steam Quality and Distribution Issues Include
- Uneven heating or insufficient heat transfer in certain areas, resulting in temperature variations or cold spots.
- Excessive condensate buildup or moisture in steam-driven equipment or processes.
- The steam pressure drops along the distribution lines, affecting the performance of steam-driven equipment.
- Audible water hammer or banging noises caused by the presence of liquid water in the steam lines.
- Premature failure of steam-driven equipment due to corrosion or erosion caused by poor steam quality.
Solutions for Improving Steam Quality and Distribution
- Addressing steam trap failures and ensuring proper condensate removal:
- Regularly inspect and test steam traps to identify any failures or malfunctions.
- Replace faulty steam traps to prevent steam leakage and ensure efficient condensate removal.
- Implement a comprehensive maintenance program to clean and maintain steam traps for optimal performance.
- Inspecting and cleaning steam distribution lines and valves:
- Conduct regular inspections of steam distribution lines to identify any blockages, scaling, or corrosion.
- Clean or descale the lines to remove any buildup that hinders steam flow and quality.
- Inspect and maintain steam control valves to ensure proper operation and minimise steam leaks.
By addressing steam trap failures, ensuring proper condensate removal, and maintaining clean steam distribution lines and valves, steam quality and distribution can be significantly improved. These solutions enhance the performance and efficiency of steam boiler systems, reduce operational issues, and prolong the lifespan of steam-driven equipment.
Combustion Issues and Flame Irregularities
Recognising Combustion Problems and Irregularities in Boiler Flames
- Combustion issues and flame irregularities in boiler systems can manifest through various signs and symptoms, including:
- Uneven or unstable flames, such as flickering or lifting off the burner.
- Excessive smoke emissions or the presence of soot on the burner or heat transfer surfaces.
- Abnormal flame colours, such as a yellow or orange hue instead of the desired blue flame.
- Inefficient combustion, resulting in reduced heat output or higher fuel consumption.
- Unusual odours, such as a strong fuel or gas smell, indicating incomplete combustion.
Troubleshooting Tips for Addressing Combustion Issues
- Checking fuel supply and adjusting burner settings:
- Ensure an adequate and consistent fuel supply, verifying fuel pressure and quality.
- Inspect and clean fuel filters, strainers, or nozzles to remove any clogs or blockages.
- Adjust burner settings, such as air-to-fuel ratio or combustion control parameters, to optimise combustion efficiency.
- Inspecting and cleaning burner components:
- Regularly inspect burner components, such as the burner head, flame retention ring, or electrodes, for damage or buildup.
- Clean or replace dirty or worn-out burner parts that may affect flame stability or combustion performance.
- Ensure proper alignment of burner components and check for any obstructions in the combustion air intake.
By diligently recognising combustion problems and irregularities in boiler flames and implementing troubleshooting measures like checking the fuel supply, adjusting burner settings, and inspecting/cleaning burner components, professionals can effectively address combustion issues. These actions help to optimise combustion efficiency, improve flame stability, reduce emissions, and ensure the safe and efficient operation of boiler systems.
Excessive Boiler Cycling and Short Cycling
Problems With Boiler Cycling
Excessive boiler cycling refers to frequent on/off cycles of the boiler, resulting in increased wear and tear on the system. This can be caused by factors such as oversized boilers, improper control settings, or excessive demand fluctuations. Short cycling, on the other hand, occurs when the boiler rapidly turns on and off in quick succession, leading to energy inefficiency and decreased system lifespan. Short cycling can be caused by undersized boilers, improperly sized or faulty controls, or rapid changes in heating demand. Both excessive boiler cycling and short cycling can lead to increased fuel consumption, decreased efficiency, and unnecessary wear on boiler components.
Solutions for Managing and Reducing Boiler Cycling
- Adjusting boiler controls and setpoints:
- Review and adjust the boiler control settings, such as on/off differentials and reset curves, to optimise boiler operation.
- Ensure that control parameters, such as temperature setpoints and pressure limits, are properly calibrated and matched to the system's requirements.
- Consider installing advanced control systems that provide better modulation capabilities and can adapt to varying heating demands.
- Implementing outdoor temperature reset controls:
- Install outdoor temperature reset controls to adjust the boiler water temperature based on the outdoor temperature.
- By modulating the boiler output in response to outdoor conditions, temperature reset controls help prevent excessive cycling during milder weather.
- Outdoor temperature reset controls can enhance system efficiency and comfort by matching the boiler's output to the actual heating demand.
By adjusting boiler controls and setpoints and adding outside temperature reset controls, professionals can reduce boiler cycling and short cycling. These methods boost the lifespan, energy efficiency, and performance of boiler systems, saving money and enhancing reliability.
Boiler Efficiency and Heat Loss
Identifying Signs of Poor Boiler Efficiency and Heat Loss
Poor boiler efficiency and heat loss can be recognized through various signs and indicators, including:
- High fuel consumption or increased energy bills without a corresponding increase in heat output.
- Inconsistent or uneven heating across the system, leading to temperature variations or cold spots.
- Excessive boiler cycling or short cycling, indicating inefficient operation.
- Excessive smoke or soot emissions, suggesting incomplete combustion and energy wastage.
- Hot surfaces or equipment near the boiler, indicating heat loss through radiation or conduction.
Solutions for Improving Boiler Efficiency and Reducing Heat Loss
- Insulating steam distribution lines and boiler components:
- Apply insulation materials to steam distribution lines, valves, and fittings to minimise heat loss during transport.
- Insulate boiler components, such as the boiler shell, flue gas outlet, and doors, to reduce radiation and convection losses.
- Regularly inspect and maintain insulation to ensure its effectiveness and integrity.
- Optimising combustion settings and conducting efficiency audits:
- Fine-tune the combustion settings, including air-to-fuel ratios and burner adjustments, to achieve optimal combustion efficiency.
- Conduct regular efficiency audits to assess boiler performance and identify areas for improvement.
- Implement proper maintenance practises, including cleaning and tuning, to ensure efficient combustion and minimise energy losses.
By implementing solutions such as insulating steam distribution lines and boiler components, optimising combustion settings, and conducting efficiency audits, professionals can improve boiler efficiency and reduce heat loss. These measures enhance energy efficiency, reduce fuel consumption, and lower operational costs. Additionally, they contribute to a more sustainable and environmentally friendly operation of the boiler system.
Safety Concerns and Malfunctioning Safety Devices
Addressing Safety Concerns and Malfunctioning Safety Devices
Safety concerns and malfunctioning safety devices pose significant risks in boiler systems. It is crucial to address these issues promptly to ensure a safe working environment. Signs of safety concerns and malfunctioning safety devices may include:
- Safety relief valves that fail to discharge or relieve pressure properly.
- Inoperative or faulty low-water cutoff devices that do not shut off the burner in the event of low water levels.
- Unusual pressure fluctuations or irregular boiler operation.
- Leakage or damage to safety devices, such as relief valves, pressure gauges, or flame safeguards.
Steps for Ensuring Proper Operation and Reliability of Safety Devices
- Testing and calibrating safety relief valves:
- Regularly test safety relief valves to ensure they open and close properly.
- Conduct pressure tests and adjust the valve settings if necessary.
- Follow manufacturer guidelines for maintenance and replacement of safety relief valves.
- Verifying proper operation of low-water cutoff devices:
- Inspect low-water cutoff devices for proper installation and connection to the boiler system.
- Test the operation of low-water cutoff devices by simulating low-water conditions and verifying their ability to shut off the burner.
- Regularly clean and maintain low-water cutoff devices to prevent clogging or malfunction.
By addressing safety concerns and ensuring the proper operation of safety devices through testing, calibration, and regular maintenance, professionals can enhance the safety and reliability of boiler systems. These measures help mitigate the risks associated with pressure buildup, low-water conditions, and other potential safety hazards. It is essential to adhere to industry standards and regulations while conducting safety checks and maintenance procedures.
Scale and Deposits Buildup
Recognising the Impact of Scale and Deposits on Boiler Performance
Scale and deposit buildup can have a significant impact on the performance and efficiency of boiler systems. It is important to recognise the consequences of scale and deposits, including:
- Reduced heat transfer efficiency due to insulating effects, leading to increased energy consumption.
- Increased fuel consumption and operating costs as the boiler works harder to compensate for reduced heat transfer.
- Risk of localised overheating and potential damage to boiler components, such as tubes, heat exchangers, and water walls.
- Decreased flow rates and pressure drop across the system, affecting overall system performance.
- Potential for corrosion and pitting due to the accumulation of corrosive substances under deposits.
Strategies for Preventing and Addressing Scale and Deposits
- Implementing proper water treatment measures:
- Use appropriate water treatment chemicals to control scaling and prevent mineral deposits.
- Regularly monitor water quality parameters, such as pH, alkalinity, hardness, and dissolved solids.
- Implement water treatment programs tailored to the specific requirements of the boiler system.
- Install water softeners or demineralisation systems to minimise mineral content in the feedwater.
- Conducting regular cleaning and descaling procedures:
- Schedule routine cleaning and descaling procedures to remove accumulated scale and deposits.
- Utilise appropriate descaling agents or mechanical methods to effectively remove deposits from heat transfer surfaces.
- Follow manufacturer guidelines and industry best practises for cleaning and descaling.
- Inspect and clean boiler tubes, heat exchangers, and other components prone to scale buildup regularly.
By implementing these strategies, professionals can prevent and address scale and deposit buildup in boiler systems. Proper water treatment measures and regular cleaning procedures help maintain optimal heat transfer efficiency, reduce energy consumption, and prolong the lifespan of boiler components. It is essential to monitor water quality regularly and follow recommended maintenance practises to mitigate the adverse effects of scale and deposits.
Preventive Maintenance and Ongoing Monitoring
The Significance of Preventive Maintenance in Preventing Boiler Issues
Preventive maintenance plays a crucial role in preventing boiler issues and ensuring the reliable and efficient operation of boiler systems. Its significance can be summarised as follows:
- Early detection and prevention of potential problems before they escalate, reducing the risk of costly breakdowns or downtime.
- Optimising boiler performance and efficiency by ensuring clean and well-maintained components.
- Prolonging the lifespan of boiler systems by addressing wear and tear and extending the longevity of critical parts.
- Enhancing safety by regularly inspecting and maintaining safety devices, relief valves, and pressure controls.
- Compliance with regulatory requirements and industry standards, ensuring adherence to safety and environmental guidelines.
Establishing a Maintenance Schedule and Monitoring Key Parameters
To implement effective preventive maintenance, it is essential to establish a maintenance schedule and monitor key parameters regularly. This can be achieved through the following actions:
- Develop a comprehensive maintenance plan that outlines the specific tasks, frequency, and responsibilities for each maintenance activity.
- Conduct routine inspections and cleaning of boiler components, such as heat exchangers, burners, safety devices, and water treatment systems.
- Monitor and record key parameters such as pressure, temperature, fuel consumption, and emissions to establish performance baselines and detect deviations.
- Implement predictive maintenance techniques, such as vibration analysis and thermal imaging, to identify potential issues before they cause significant problems.
- Maintain accurate documentation of maintenance activities, including repairs, replacements, and inspections, to track the history and condition of the boiler system.
By emphasising preventive maintenance and ongoing monitoring, individuals and organisations can proactively address potential boiler issues, optimise performance, and extend the lifespan of boiler systems. Regular maintenance, inspections, and monitoring of key parameters enable early detection of problems, facilitate timely interventions, and promote the safe and efficient operation of boilers.
Professional Assistance and Consulting Experts
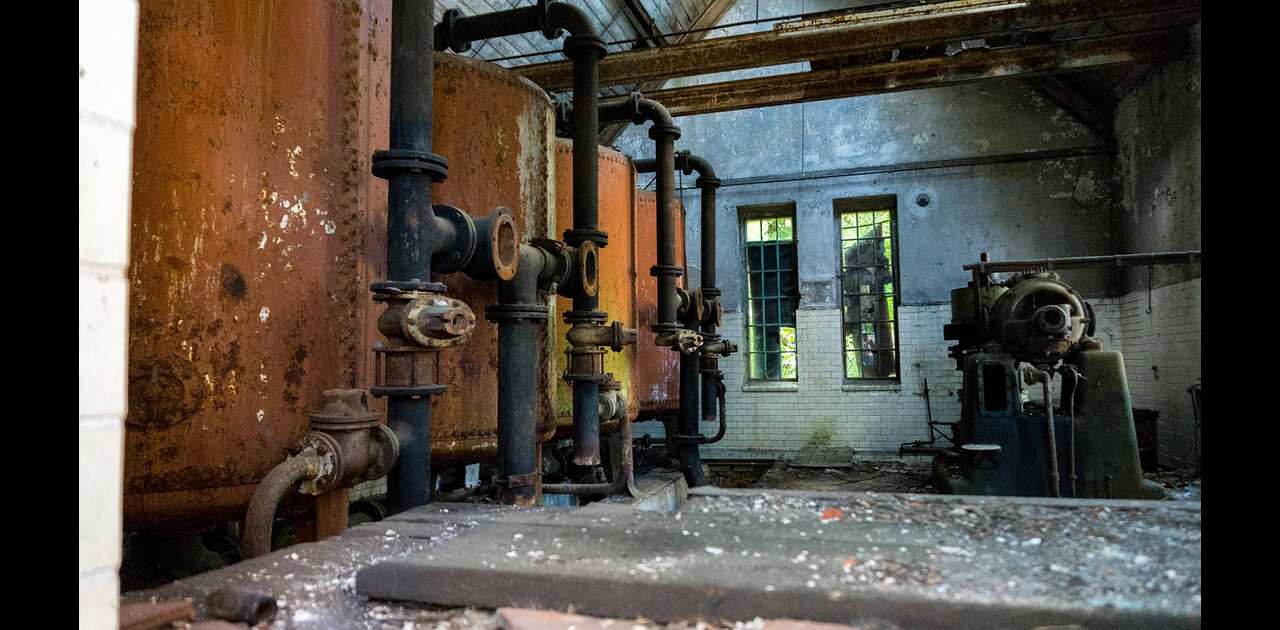
When to Seek Professional Assistance for Complex Boiler Issues
While many boiler issues can be addressed through routine maintenance and troubleshooting, there are instances when professional assistance is necessary. It is important to know when to seek expert help, including:
- Complex and recurring problems that cannot be resolved through standard troubleshooting methods.
- Safety concerns, such as malfunctioning safety devices or high-pressure situations that require immediate attention.
- Boiler performance issues that persist despite adjustments and maintenance efforts.
- Compliance with industry standards, regulations, and inspections requiring the expertise of professionals.
- Upgrades or modifications to the boiler system that necessitate specialised knowledge and skills.
Importance of Consulting Experts and Boiler Service Providers
Consulting experts and engaging the services of reputable boiler service providers offer several advantages, including:
- Specialised knowledge and expertise in boiler systems, ensuring accurate diagnosis and effective resolution of complex issues.
- Access to advanced tools, technologies, and resources that may not be available to non-professionals.
- Compliance with safety regulations and industry standards, minimising the risk of accidents or non-compliance.
- Preventive maintenance and proactive strategies to optimise boiler performance, reduce downtime, and extend system lifespan.
- Peace of mind, knowing that the boiler system is in the hands of professionals who prioritise safety, efficiency, and reliability.
By recognising the need for professional assistance in complex boiler issues and consulting experts or boiler service providers, individuals and organisations can ensure the proper functioning and longevity of their boiler systems. The expertise and resources offered by professionals help address challenges effectively, mitigate risks, and optimise the performance of boiler systems.
Troubleshooting steam boiler systems is vital for their maintenance. This article covered common issues like low water level, poor steam quality, combustion irregularities, excessive cycling, heat loss, safety concerns, and scale buildup. Seeking professional assistance, preventive maintenance, and ongoing monitoring are key. By implementing these measures, individuals can ensure efficient and productive boiler system operation