Boiler Systems and Their Applications
The symbiotic link between steam and boilers is a keystone in the domain of industrial processes, enabling a wide range of sectors such as manufacturing, energy production, food processing, and more. Within boiler systems, the intricate interaction of heat, pressure, and fluid dynamics generates the transformative power of steam, a medium with unequalled potential to transport energy, facilitate mechanical labour, and drive critical processes. This comprehensive talk delves into the intricate science that regulates boiler systems to illuminate the heart of steam-driven technologies. Through a thorough investigation, this essay tries to demystify the complicated mechanisms underpinning steam generation, illuminate the basic principles regulating boiler operation, and show the significant significance of this symbiotic partnership in varied industrial applications.
The Basics of Steam
Introduction to Steam: A Gaseous State of Water
Steam, an amazing and versatile chemical, lies at the heart of many industrial operations. The application of thermal energy converts water from a liquid to a gaseous state, resulting in the generation of steam. This is not a typical transition; it necessitates a fine balance of energy exchange and molecular interactions. The kinetic energy of the molecules in water increases when it is heated, allowing them to break free of their liquid connections and convert into the vaporous state of steam. This transformation represents not only a change in physical condition, but also a fundamental shift in the underlying qualities of the substance, making it a vital agent in a range of industrial processes.
Understanding the Properties and Characteristics of Steam
Steam's various applications are based on its features and characteristics. Steam, unlike liquids, is expansive and has the ability to apply tremendous force due to the kinetic energy of its gaseous molecules. Temperature, pressure, and volume interact dynamically in a ballet regulated by thermodynamic principles. Understanding the different phases of steam (saturated steam and superheated steam) is essential for understanding its properties and applications. Saturated, latent-heat-saturated steam can exist in thermal equilibrium with its liquid state at a specific temperature and pressure. Superheated steam, on the other hand, which has absorbed additional heat beyond its saturation point, has properties distinct from saturated steam and offers advantages in a variety of applications.
Steam tables, which specify these qualities across several phases, carefully manage the relationship between steam's temperature and pressure. This connection is crucial in engineering calculations because it allows for precise predictions of steam behaviour in varied systems. Understanding the latent heat of vaporisation of steam, or the energy required for its phase shift, is critical to understanding its role as an energy carrier. Taking advantage of these features allows engineers and operators to maximise the use of steam, tailoring it to a variety of activities such as power generation and mechanical propulsion, as well as heating and sterilising procedures.
Understanding steam entails more than simply viewing it as a consequence of heat and water. It instead displays a dynamic entity with inherent qualities that dictate its behaviour and applicability. Exploring the complicated interplay between temperature, pressure, volume, and latent heat reveals steam's infinite powers as a versatile agent in industries.
Principles of Heat Transfer
Overview of Heat Transfer Mechanisms: Conduction, Convection, and Radiation
In the study of thermal dynamics, the concepts of heat transfer form the cornerstone of our understanding of energy distribution. Heat, a kind of energy that naturally moves from higher to lower temperatures, is governed by three main mechanisms: conduction, convection, and radiation. Conduction occurs within solids or stationary fluids when vibrational energy is transferred from one molecule to another, propagating heat via direct molecular contact. Convection, on the other hand, happens in fluids (liquids or gases) where warmer, less dense parts rise and cooler, denser regions descend, resulting in a fluid motion cycle that redistributes heat. Radiation, the only method capable of transporting heat in a vacuum, comprises a warmer surface emitting electromagnetic waves that are absorbed by cooler surfaces, transferring heat without the use of a solid medium. These heat transfer principles underpin the behaviour of matter and energy in various systems, offering light on the intricate processes that govern our world.
Applying Heat Transfer Principles to Steam Generation in Boilers
Understanding heat transfer mechanisms is critical for unravelling the complicated art of steam generation within furnaces. The process of transforming water into steam is a symphony of various processes, all carefully arranged for maximum efficiency and safety. Conduction is critical in transporting heat from the combustion process to the water-filled tubes within the limitations of the boiler's significant structure. When flames come into contact with the outside surface of these tubes, heat transfers via conduction, boosting the temperature of the water and causing it to change into steam.
Meanwhile, convection occurs as heated water within the boiler tubes becomes less dense and rises, to be replaced by cooler water that undergoes its own heat absorption and ascent. By spreading heat equally throughout the water volume, convective circulation promotes uniform steam production. Heat emanating from the high-temperature environment of the combustion chamber to the surrounding water-bearing components also contributes. This radiant radiation serves as an extra heat source for the creation of steam.
The union of heat transfer mechanisms within boilers emphasises the importance of rigorous design, engineering, and control in the complex tapestry of steam generation. Conduction, convection, and radiation all work together to turn water's latent energy into steam's kinetic energy. Achieving a balance between these systems allows for the efficient and secure production of steam. Engineers and operators develop a deep grasp of the interplay at the heart of steam-dependent industrial processes by diving into these concepts, establishing the framework for optimal performance and productivity.
Steam Generation Process
The science and art of producing steam in furnaces is a complicated process that involves thermodynamics and fluid dynamics. This complicated ballet culminates in the transformation of water into steam, which is the lifeblood of many industrial operations. Within boilers, the steam generation process is comprised of a succession of precisely staged processes, each of which plays a critical part in harnessing the latent energy held within water and translating it into a powerful source of mechanical force.
Within the limits of a boiler, the transformation of water into steam is a complex process guided by several stages. The heating phase marks the start of this transition. The temperature of the water begins to rise as combustion or other sources of heat energy are introduced. This rise in temperature imparts kinetic energy to water molecules, causing them to oscillate with increasing vigour and velocity. Conduction and radiation mechanisms, respectively, promote the passage of heat from the source to the water at this point.
The transformation of water from a liquid to a gaseous state takes centre stage during vaporisation, which occurs shortly after heating. The energy injection overcomes the molecular forces that keep water in its liquid state as the temperature of the water reaches its boiling point. This bonding breakdown causes water molecules to split, resulting in the creation of steam droplets. The dynamic interaction of convection and conduction guarantees equitable distribution of heat, promoting a controlled and homogeneous transformation of water into steam.
The process of steam generation can finish with simple vaporisation, but oftentimes the final stage of this transition is superheating, which raises the temperature of the steam above the saturation point. This stage generates steam with a higher energy potential, making it more adaptable for applications that require precise temperature and energy control. Superheated steam has advantageous features due to its ability to carry more energy, which increases its efficiency and efficacy in a range of industrial applications.
The production of steam in boilers takes place in a number of well-defined stages guided by thermodynamic and heat transport principles. Water's metamorphosis into steam shows the symbiotic relationship between scientific understanding and technical prowess as it crosses the domains of heating, vaporisation, and superheating. This complex process not only fuels industrial processes, but it also symbolises the never-ending quest for efficiency and innovation in the goal of exploiting nature's latent energy.
Boiler Components and Function
A boiler system, the heart of steam generation, is a complicated assembly comprised of a number of critical components, each precisely constructed to fulfil specialised roles in tandem. The interaction of these ingredients results in the controlled and efficient conversion of water into steam, which fuels a wide range of industrial uses. Anatomy of a boiler system reveals a complex interaction of engineering brilliance and scientific concepts, culminating in a flawless synthesis of thermodynamics and mechanical prowess.
Exploring the Functions of Each Component
- Shell: The central vessel contains both water and steam, providing a closed environment where heat transfer occurs to produce steam.
- Furnace/Combustion Chamber: This is where the combustion process takes place. Fuel, such as coal, oil, or gas, is ignited to generate high temperatures that transfer heat to the water or tubes surrounding it.
- Burners: These devices are responsible for precisely mixing the fuel and air in the right proportions, ensuring efficient and complete combustion for maximum heat generation.
- Grates/Stokers: In boilers using solid fuels, grates or stokers are mechanisms that evenly distribute the fuel across the furnace. This ensures efficient combustion and prevents clumping that might impede airflow.
- Water Tubes: Tubes placed within the furnace carry water, which is heated by the combustion gases. The heat transfer from the gases to the water generates steam within the tubes.
- Steam Drum: This vessel collects the steam generated in the water tubes. It serves as a reservoir, allowing the steam to separate from any remaining water before being distributed to the rest of the system.
- Water Drum: The water drum stores a reserve of water that can be supplied to the water tubes as needed to maintain a consistent water level within the boiler.
- Economizer: This heat exchanger preheats the water before it enters the main boiler components using the waste heat from the exhaust gases. This enhances overall system efficiency.
- Superheater: Beyond the initial boiling point, the steam passes through the superheater, which raises its temperature and energy content. This superheated steam is used for specific industrial processes and is not always included.
- Air Preheater: By transferring heat from the exhaust gases to the incoming combustion air, the air preheater enhances combustion efficiency and reduces fuel consumption.
- Boiler Feed Pump: This pump ensures a constant supply of water to the boiler, maintaining the appropriate water level for safe and efficient operation.
- Steam Separator/Cyclone Separator: As the steam leaves the water in the steam drum, any remaining water droplets are separated from the steam before it enters the steam distribution system.
- Safety Valves: These valves are crucial safety devices that automatically release excess pressure from the boiler to prevent catastrophic explosions.
- Pressure Gauge: This instrument measures the internal pressure of the boiler, allowing operators to monitor and maintain safe operating conditions.
- Temperature Gauges: Various temperature gauges provide readings of water and steam temperatures at different points within the system, aiding in control and monitoring.
- Water Level Indicator/Gauge Glass: The level of water within the boiler is visually indicated by a gauge glass, allowing operators to ensure that water levels remain within safe limits.
- Blowdown Valve: This valve is used to periodically discharge a small amount of water from the boiler to remove accumulated impurities and maintain water quality.
- Control System: The control system regulates various parameters, including temperature, pressure, and fuel input, ensuring stable and efficient boiler operation.
- Chimney/Stack: This component expels combustion gases and steam into the atmosphere, helping to prevent pollution within the operational environment.
- Insulation: Insulating materials are used to reduce heat loss from the boiler, improving overall energy efficiency.
- Deaerator: This device removes dissolved gases, such as oxygen, from the feedwater to prevent corrosion within the boiler system.
- Feedwater Heater: By preheating the feedwater using extracted steam, the feedwater heater improves overall efficiency by utilising waste heat.
- Piping and Valves: The network of pipes and valves transports water, steam, and other fluids within the system, allowing for controlled distribution and regulation.
- Instrumentation: Various sensors, switches, and indicators provide real-time operational data, aiding operators in monitoring and managing the boiler's performance.
- Control Panel: The control panel serves as the interface through which operators can monitor and adjust various aspects of the boiler's operation, ensuring safe and optimal performance.
The intricate choreography of a boiler system's components harmoniously intertwines to yield the controlled and efficient generation of steam. From the stalwart boiler shell and combustion-driven furnace to the heat exchangers, feedwater system, and myriad safety features, each element plays an indispensable role in transforming raw materials into a potent source of energy. This orchestration epitomises the fusion of engineering precision and scientific insight, culminating in a powerful embodiment of applied thermodynamics that drives industrial progress.
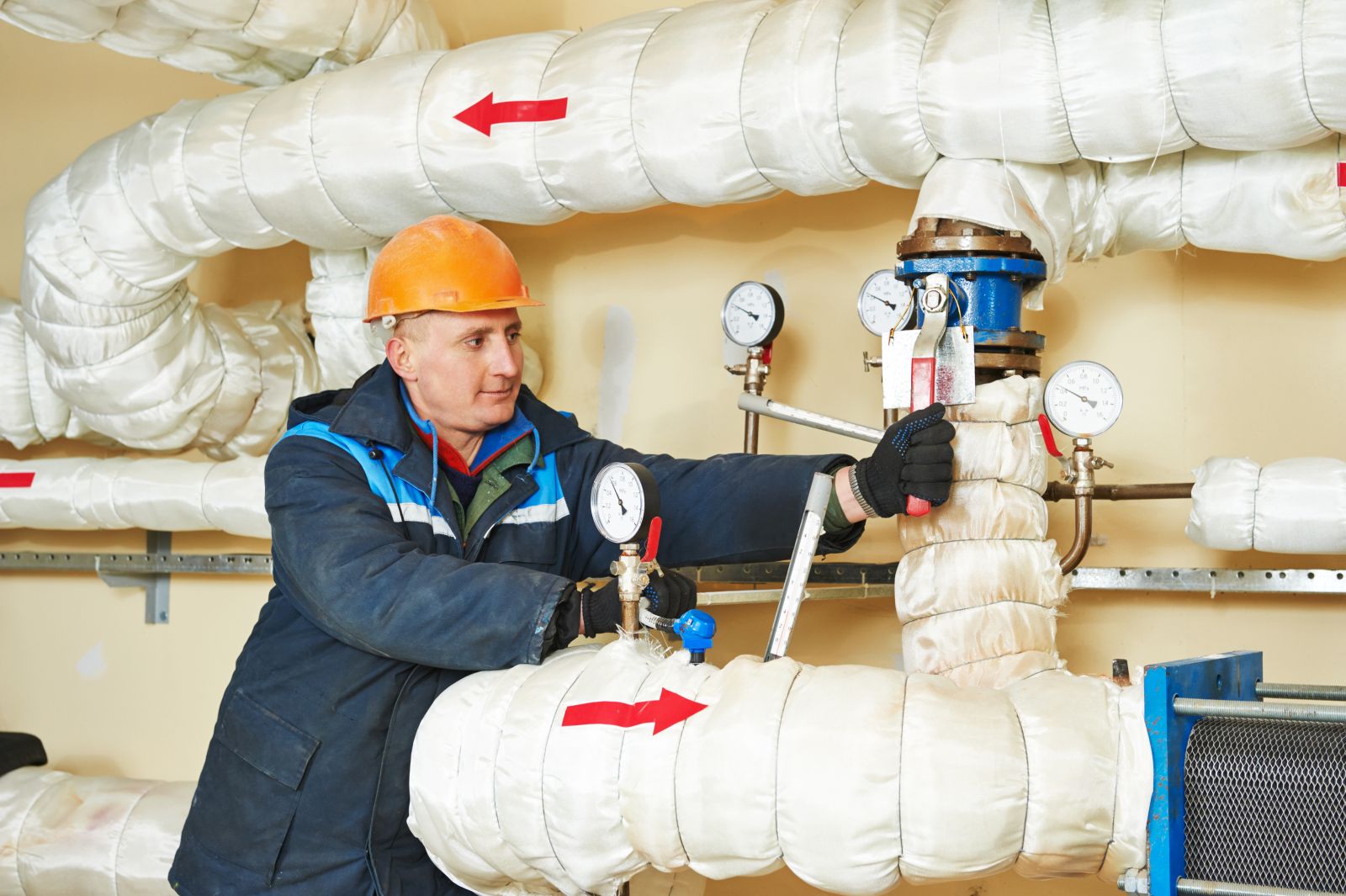
Types of Boilers
- Fire-Tube Boilers: These boilers contain a water-filled cylinder casing and passageways that carry hot gases from the boiler. Heat is passed through the tube walls, heating the water and producing steam. Fire-tube furnaces are small, easy to install, and ideal for smaller applications. Because of its simplicity and versatility to control fluctuations in steam demand, fire-tube boilers are used in heating systems, small-scale industrial processes, and applications requiring quick steam generation. Their design, however, limits their ability to endure higher pressures and more complex fuel mixes.
- Water-Tube Boilers: In contrast to fire-tube boilers, water-filled tubes circulate around the combustion chamber in water-tube boilers. These tubes transport heat from hot gases to water. Water-tube boilers, which are commonly used in bigger industrial settings, give increased efficiency and capacity. Water-tube boilers are used in power generation, large-scale industrial processes, and applications that require precise control of steam characteristics. They provide superior steam quality, higher efficiency, and the ability to handle high pressures.
- Electric Boilers: These furnaces use electricity to generate heat, removing the need for combustion. They are pure, efficient, and suitable for applications involving emissions or fuel storage. These furnaces are adjustable, produce no emissions, and give on-demand heating. They are commonly employed in laboratories, hospitals, and small-scale companies where space and emissions are limited.
- Cyclone-Fired Boilers: This unique design employs a cyclone combustion chamber in which fuel and air are mixed and burned in a vortex, resulting in efficient combustion and lower emissions. Because of their efficient combustion and low emissions, cyclone-fired boilers are ideal for coal-fired power generation and applications requiring greater combustion control.
The choice of boiler type is influenced by capacity, efficiency needs, fuel availability, and pollution laws. Understanding the distinct characteristics of each type enables enterprises to select the boiler that best suits their operational needs.
Combustion and Fuel Considerations
The basic mechanism underpinning the creation of energy in boilers is combustion, which is the regulated chemical interaction between fuel and oxygen. This delicate dance of fuel, air, and ignition produces heat energy, which powers the formation of steam. Fuel, the basic substance of combustion, includes traditional fossil fuels like coal, oil, and natural gas, as well as renewable sources like biomass and even waste materials. When fuel is coupled with a suitable amount of oxygen from the air, it undergoes oxidation, releasing energy in the form of heat. The ignition process, which is typically triggered by a spark or pilot flame, acts as a catalyst to ignite the fuel-air mixture, kicking off the chain reaction that continues combustion.
Fuel Options and Their Combustion Characteristics in Boilers
- Coal: A traditional fossil fuel, coal offers a high energy density and has long been a staple in power generation. However, its combustion releases pollutants, necessitating advanced technologies for emissions control.
- Oil: Liquid fuels, such as diesel and heavy fuel oil, are known for their convenience and ease of transport. They exhibit efficient combustion characteristics, making them suitable for applications where emissions standards are well-maintained.
- Natural Gas: Clean-burning and readily available, natural gas is favoured for its low emissions and efficient combustion. It is widely employed in both industrial and residential settings.
- Biomass: Renewable biomass fuels, derived from organic materials like wood, agricultural residues, and even algae, are gaining traction due to their sustainability. However, their combustion characteristics can vary significantly, requiring careful boiler design and operational adjustments.
- Waste-to-Energy Fuels: Waste materials can be used as fuels in boilers, contributing to waste management and energy production. However, their combustion properties can be challenging to predict due to the heterogeneity of waste streams.
The availability, cost, emissions standards, and sustainability goals all have a role in fuel selection. Understanding the combustion characteristics of each fuel type is critical for ensuring optimal performance, efficiency, and compliance with environmental requirements. Boiler systems must be precisely constructed to accommodate the unique properties of the chosen fuel, assuring safe and efficient combustion while lowering emissions. In the ever-changing landscape of energy production, combustion science and careful evaluation of fuel sources remain critical in crafting a future that is both sustainable and efficient.
Boiler Efficiency and Performance
In the field of energy production, the efficiency with which a boiler system turns fuel into usable heat energy is a critical measure. It is a multidimensional concept influenced by a variety of factors, each of which contributes to the overall performance of the system. Combustion efficiency, for example, assesses how well fuel is converted into thermal energy while leaving no unburned products behind. Heat transfer efficiency, on the other hand, assesses the effectiveness of heat transmission from the combustion process to water or steam. This comprises both conduction inside boiler components and fluid convection.
Losses within a boiler system are also important in determining its performance. These losses include stack losses (heat transferred by flue gases) and radiation losses from the boiler's exterior. Reduced losses from well-designed insulation and excellent flue gas management contribute significantly to total efficiency. In essence, boiler efficiency is a complex interaction of several parameters, which define a boiler system's ability to extract the maximum energy potential from its fuel.
Exploring Methods to Improve Boiler Efficiency and Performance
- Optimised Combustion: By precisely controlling the fuel-air mixture, optimising combustion air supply, and ensuring complete combustion, the overall efficiency of the system can be significantly improved. Regular maintenance, such as cleaning burners and adjusting combustion parameters, is crucial to sustaining optimal performance.
- Efficient Heat Transfer: Regular inspection and cleaning of heat exchanger surfaces prevent the buildup of deposits that impede heat transfer. Implementing technologies like soot blowers, which remove accumulated ash and debris, enhances heat exchange efficiency.
- Condensing Boilers: These advanced boilers recover heat from exhaust gases by condensing water vapour present in the flue gases. This process not only boosts efficiency but also reduces emissions.
- Waste Heat Recovery: Capturing waste heat from various processes, such as exhaust gases or hot water streams, and using it to preheat feedwater or other fluids can significantly improve overall efficiency.
- Upgrading Controls and Automation: Advanced control systems and automation technologies ensure that boilers operate optimally under varying conditions, adjusting combustion parameters and other variables for peak efficiency.
The pursuit of higher boiler efficiency and performance needs a multifaceted, holistic strategy. Industries can adopt a variety of methodologies and technologies to improve boiler system efficiency by understanding the intricacies of combustion, heat transmission, and losses. The pursuit of greater efficiency not only decreases fuel consumption and operational expenditures, but it also helps to resource sustainability and the reduction of environmental effect.
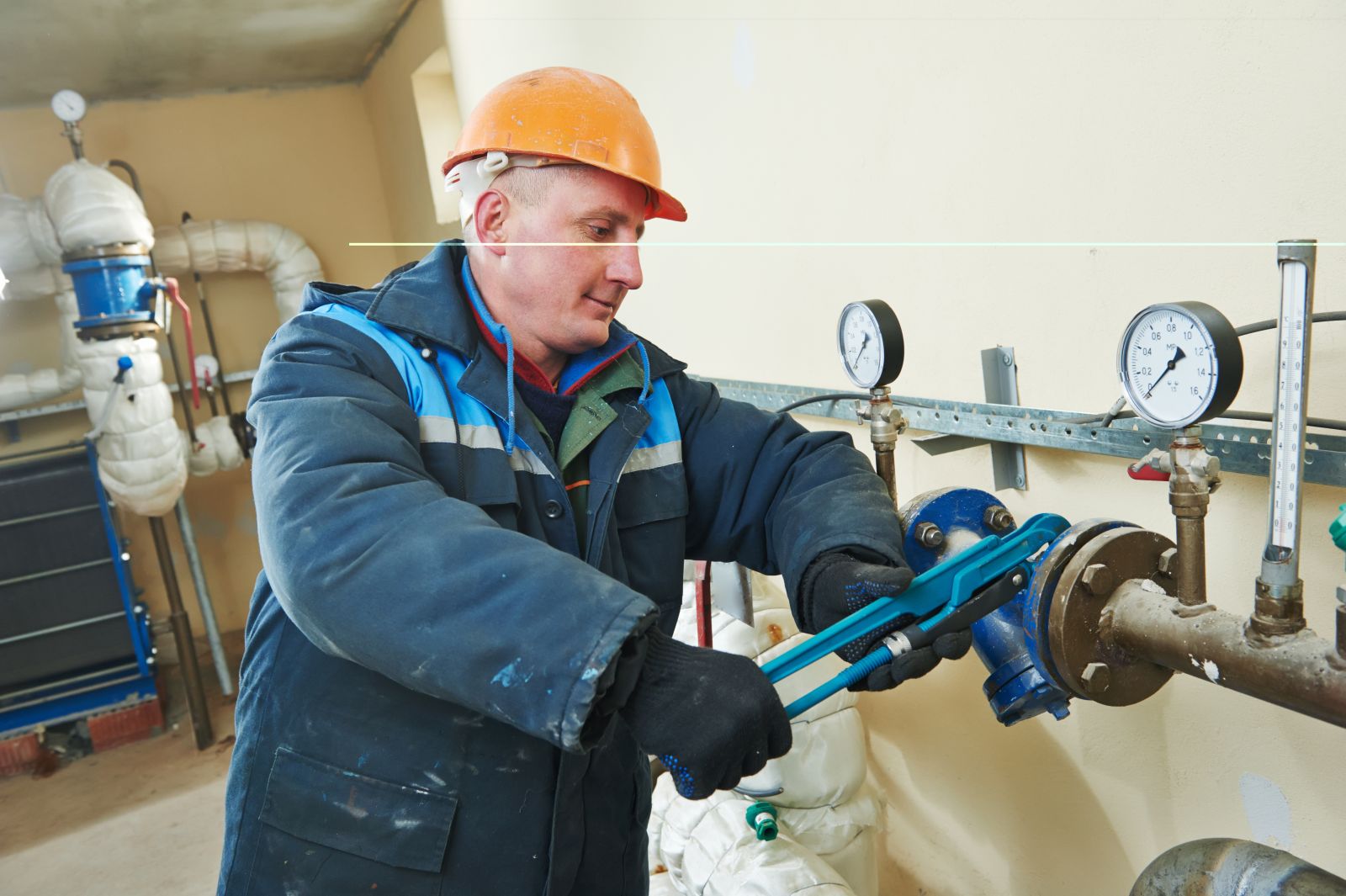
Steam Applications in Various Industries
Steam has been instrumental in revolutionising worldwide power generation. Steam-based power plants have been the backbone of electricity generation in the energy sector for decades. Water is typically heated to generate steam, which powers turbines to generate mechanical energy. This mechanical energy is converted into electricity via generators. Steam turbines are used in a variety of power plants due to their efficiency and scalability, including coal-fired, natural gas, nuclear, and even renewable sources such as concentrated solar power systems. Because of their ability to transform thermal energy into mechanical labour with minimal waste, steam turbines have become crucial for dependable and regular power generation.
Exploring Steam Utilisation in Industrial Processes, Heating, and Cooling Systems
Steam is used in a range of industrial operations, as well as heating and ventilation systems, in addition to power generation. Steam is a flexible and necessary tool in a wide range of industrial operations, including sterilisation, pasteurisation, and drying. Steam is used in the food and beverage industries to assure product safety and extend expiration dates. Furthermore, the remarkable heat transfer capabilities of steam are used for industrial heating. Using steam furnaces for space heating, raising the temperature of fluids in processes, and producing steam for mechanical work all at the same time enhances energy efficiency and reduces emissions in industrial settings.
Steam's versatility extends to refrigeration systems as well. Steam ejectors or steam-driven chillers facilitate cooling by utilising the pressure differential between steam and the surroundings. This environmentally friendly cooling approach is used in air conditioning and refrigeration systems, giving a sustainable alternative to conventional cooling methods that use synthetic refrigerants with higher environmental implications.
Steam applications are important in many areas, from powering the planet through efficient energy generation to serving as the cornerstone of industrial processes, heating, and ventilation systems. As technology improves, breakthroughs in steam utilisation are likely to persist, enabling advances in energy efficiency and sustainability across a wide range of industries.
Safety Considerations in Boiler Systems
Because of the high pressure and temperature conditions under which they work, boiler systems, which are crucial in many sectors, pose inherent hazards. It is critical to identify and eliminate potential dangers in order to ensure the safety of employees and the durability of equipment. One of the biggest concerns is the potential of detonation owing to the building of excess pressure. Routine inspections and maintenance, as well as the installation of pressure release valves, are critical defences against catastrophic catastrophes. Adequate ventilation and periodic purging of combustion chambers aid in the prevention of flammable gas accumulation.
Furthermore, when working with steam systems, the risk of scalding or burning is a big worry. Operators must be cautious around hot surfaces and pipes. Accidents can be considerably reduced by using personal protective equipment (PPE) and effective training sessions. Lockout/tagout protocols guarantee that boilers are shut off and depressurized prior to any servicing, preventing inadvertent restarts and protecting staff.
Exploring Safety Devices and Regulations for Boiler Systems
To improve boiler safety, modern boiler systems incorporate a number of innovative safety measures. Through real-time monitoring, pressure and temperature gauges enable operators to maintain safe operating conditions. Low-water cutoff devices are essential for preventing harm caused by low water levels. When water levels fall below a predetermined level, these devices automatically shut down. Flame prevention systems monitor the combustion process and shut down the system if any irregularities are discovered.
Furthermore, tight laws and standards play an important part in boiler safety. In the United Kingdom, the Health and Safety Executive (HSE) enforces guidelines controlling the design, installation, operation, and maintenance of furnace systems. Compliance with these standards is required to avoid accidents and legal ramifications. Regular inspections, tests, and certification by recognised bodies ensure that boiler systems meet the required safety standards.
A comprehensive safety approach is required when dealing with boiler systems. Understanding and reducing possible dangers through rigorous maintenance, operator training, and the use of safety devices are critical elements in protecting both personnel and equipment. Compliance with established requirements underscores the commitment to ensuring a safe working environment in boiler-dependent sectors.
Innovations and Advancements in Boiler Technology
Boiler technology has made tremendous advances in industrial engineering in recent years, with the goal of improving efficiency, safety, and sustainability. Design developments have resulted in the development of compact, modular boiler systems with increased installation flexibility and scalability. These systems use cutting-edge materials, such as high-strength alloys and corrosion-resistant compounds, to extend boiler operational lifetime while reducing maintenance requirements.
The incorporation of modern control technology has also transformed boiler operation. Digital controls optimise combustion processes, fuel economy, and heat distribution by frequently employing advanced algorithms and machine learning. This results in increased system efficiency, lower energy consumption, and lower emissions. Furthermore, real-time monitoring and predictive maintenance capabilities let operators spot possible faults before they escalate, improving overall operational dependability.
Exploring Advancements in Efficiency, Emissions Reduction, and Sustainability
Significant progress has been achieved in the efficiency, emissions reduction, and sustainability of furnace technology. Condensing technology in modern boilers allows for the recovery of heat from flue gases, increasing overall thermal efficiency. Combined Heat and Power (CHP) systems, which combine boilers and electricity generation, improve efficiency by using waste heat to generate electricity, lowering energy consumption and emissions.
Environmental concerns and legal requirements have pushed emission reduction to the forefront of innovation. The incorporation of low-NOx burners and selective catalytic reduction systems into furnaces minimises nitrogen oxide emissions while also contributing to improved air quality. Alternative fuels such as biomass and hydrogen are gaining traction, allowing for cleaner combustion processes and reducing dependency on fossil fuels.
Sustainability lies at the heart of these advancements as boiler technology aligns with worldwide aspirations to create a sustainable future. Increasing efficiency lowers resource usage and the carbon footprint. Furthermore, incorporating renewable energy sources into boiler setups, such as solar thermal systems, aids sustainability objectives. As technology advances, the trajectory of boiler advancements indicates a balance between industrial progress and environmental protection.
Recent improvements in boiler technology show a paradigm change towards greater efficiency, lower emissions, and long-term sustainability. This discipline's progress promises to transform industry while tackling significant environmental challenges. The possibility of a more sustainable and productive future grows as sectors continue to incorporate these advancements.
Future Outlook and Emerging Trends
Steam and furnace system advances in the future will reshape industrial processes, energy efficiency, and environmental resilience. One of the anticipated advances is the integration of sophisticated sensors and monitoring systems. These devices will provide real-time data on furnace performance, fuel consumption, emissions, and the health of the equipment. Operators can use predictive analytics and machine learning algorithms to identify future difficulties, optimise combustion processes, and reduce downtime, resulting in increased efficiency and lower operational costs.
Furthermore, the incorporation of alternative fuels is expected to gain significance. Boiler systems will place a greater emphasis on the use of renewable and low-carbon fuels, such as hydrogen and biogas, as companies strive for better sustainability. These fuels, in addition to lowering greenhouse gas emissions, have the potential for energy storage and demand response, further aligning them with the growing energy landscape.
The convergence of cutting-edge technologies with the ability to change the industrial landscape will define the future of steam and furnace systems. The road ahead has the potential to change how industries generate energy, decrease emissions, and ensure operational excellence, from predictive maintenance enabled by data analytics to the incorporation of renewable fuels and the emergence of smart furnaces. Steam and boiler systems will continue to play an important role in fostering sustainable industrial development as these trends evolve.
In Conclusion
Finally, the complicated physics underpinning steam and furnace systems has propelled businesses to previously unheard-of levels of efficiency, safety, and sustainability. This science has enabled the revolutionary harnessing of thermal energy, from the fundamental concepts of heat transmission and phase transition to the detailed engineering of boiler designs. Steam technology's adaptability, as demonstrated by its effective applications in power generation, industrial operations, heating, and cooling, among other sectors, proves its pervasiveness across industries.
When we contemplate the diverse function that steam and boiler systems play in modern civilization, it is apparent that their importance goes far beyond that of basic machinery. These systems are critical to industrial operations and help to improve product quality, conserve energy, and protect the environment. They demonstrate the connection between scientific knowledge and technical innovation.
It is critical to highlight the extraordinary improvements made possible by steam and furnace technology in the search of a greener and more efficient future. Aspiring engineers, scientists, and industry professionals are urged to learn more about the basics of steam generation and boiler systems. We can unlock more of these technologies' potential by examining their intricacies, resulting in innovations that will impact our industries, economies, and the greater global landscape. The world of steam and furnaces provides countless potential for discovery and invention, promising a more sustainable and affluent future.