Guide for Choosing the Right Boiler Supplies
The most important thing you can do to ensure that your heating system works properly and lasts a long time is to choose the right boiler materials. The job may appear difficult, but with the appropriate assistance, you can make wise decisions that will have a significant impact on how effectively your boiler performs. In this article, we'll try to offer you a complete picture of the most significant factors to consider when selecting boiler supplies, from the most critical parts to the most recent advancements in the area. We want to give you the information you need to find the best boiler supplies for your industry’s needs.
Assessing Your Business Needs
One of the most crucial initial stages in selecting the proper boiler products for your business is to study as much as you can about your industry and the needs of your application. Each firm has unique heating requirements, whether for heating areas, producing steam, or running industrial processes. Learning more about your sector can help you identify the key obstacles and opportunities that will influence how you select boiler supplies. This will assist you in ensuring that the equipment you select is precisely suited to your business objectives. Understanding these guidelines can not only improve the performance of your heating system, but it will also save you money and benefit the environment.
To make wise decisions, you must first understand the most crucial aspects of selecting boiler supplies. Many factors must be considered, including the type of boiler, its size, the source of the fuel, and the pollution regulations. Each of these factors has a direct impact on how well the boiler system operates. Choosing the correct sort of boiler for your application, for example, can have a significant impact on how productive your firm is and how much energy it consumes overall. It is also critical to consider the maintenance requirements, safety features, and cost implications of the chosen boiler supplies to ensure that they will work properly and survive for a long period. You'll be able to ensure that your boiler system suits your budget and your business's needs while also fulfilling industry standards and environmental rules if you take a close look at these elements.
One of the most crucial tasks in selecting boiler supplies is to conduct a thorough analysis of your company's requirements. This investigation looks at how well your current heating system works, how much energy it consumes, and whether or not there are any inefficiencies. Also, consider how your company will expand and evolve in the future so that the boiler goods you select can keep up with changing needs. Hiring skilled consultants who can perform extensive energy audits and make customised recommendations adds a lot of value and assists you in making sound decisions. You can ensure that your boiler system matches your company's needs by considering factors such as production rate and seasonal fluctuations. Finally, a thorough examination of your company's requirements will ensure that the boiler supplies you select best fit your changing requirements and help your company run smoothly and for a long time.
Types of Boilers
Because they create critical volumes of heat or steam, industrial boilers are critical components of many industrial processes. These boilers are available in a range of configurations, each designed to satisfy specific operational requirements and industry standards. Businesses must have a solid awareness of the many types of industrial boilers in order to make informed judgements about their energy needs and operational efficiency. Some common industrial boiler types are as follows:
Fire Tube Boilers
The fire tube boiler is one of the most common types of industrial boilers. They are made out of a cylinder-shaped water-filled shell with tubes running through it. Hot combustion byproduct gases that heat the water are transported through these tubes. In general, fire tube boilers are tiny, easy to use, and suitable for applications that require little steam. However, they are less effective than other types and may not be suitable for high-pressure applications.
Water Tube Boilers
Because of their higher efficiency and ability to resist high pressures, water tube boilers stand out. These boilers have a system of tubes filled with water through which hot gases heat the water. Due to their larger surface area for heat transfer and ability to withstand high steam pressures, water tube boilers are perfect for industrial processes that demand massive quantities of steam at high pressures. They are frequently used in steam-intensive industries and power generation.
Electric Boilers
Electric boilers use electricity as their main energy source to heat water and produce steam. They require very little maintenance, are incredibly efficient, and produce no emissions when in operation. For applications requiring low emissions and constrained space, electric boilers are perfect. They frequently work in places with dependable and affordable power.
Steam Boilers for Process Heating
Process heating steam boilers are created to specifically fulfil the needs of a given industrial operation. These boilers can come in a wide variety of designs, fuel types, and capacities. They frequently work in sectors including textile production, chemical manufacturing, and food processing. The required steam pressure, temperature, the availability of fuel, and the desired level of energy efficiency all play a role in determining the type of boiler that is utilised.
Each type of industrial boiler has its own advantages in terms of efficiency, capacity, and fuel sources and can be used for a variety of industrial purposes. The best sort of boiler is chosen based on factors such as particular operating needs, resources that are accessible, and the desired level of energy efficiency. When choosing the optimum boiler type for their processes, businesses should carefully consider their requirements and consult with industry experts to ensure optimal performance and cost-effectiveness.
Determining Steam Capacity
A critical step in ensuring that a boiler can handle the steam requirements of a particular industrial operation while retaining optimal efficiency is determining the steam capacity of industrial boilers. A thorough examination of all the variables that affect steam generation and consumption is required for an accurate steam capacity estimate. The following are important factors to take into account when calculating the steam capacity for industrial boilers:
- Process Requirements: The amount of heat energy needed for the industrial process that the boiler is used for essentially determines how much steam it can produce. For an accurate capacity assessment, it is crucial to comprehend the process's peak steam demand, fluctuations, and variations in steam consumption. Industries might have very different process needs, ranging from intermittent and variable loads to steady and continuous demand.
- Load Analysis: The thermal energy required to heat raw materials, create steam, and maintain appropriate process temperatures must be evaluated when performing a thorough load analysis. To make sure that the chosen boiler can supply appropriate steam capacity during both regular and peak operating conditions, factors including batch processing, start-up procedures, and fluctuations in production rates must be taken into consideration.
- Steam Pressure and Temperature: The capacity of the boiler is directly impacted by the steam pressure and temperature needed for industrial operation. Larger steam capacity is frequently required to meet the increased heat energy requirements caused by higher pressure and temperature requirements. To obtain the best process performance and safety, it is crucial to balance the desired pressure, temperature, and steam generation capacity.
- Safety Margins and Efficiency: When calculating steam capacity, safety margins must be taken into account. A boiler may have inefficient combustion, decreased energy efficiency, and potential safety risks if it is loaded over its rated capacity. By ensuring that the chosen boiler has a margin above the estimated steam capacity, one can account for unforeseen events and prevent working the boiler to its maximum capacity.
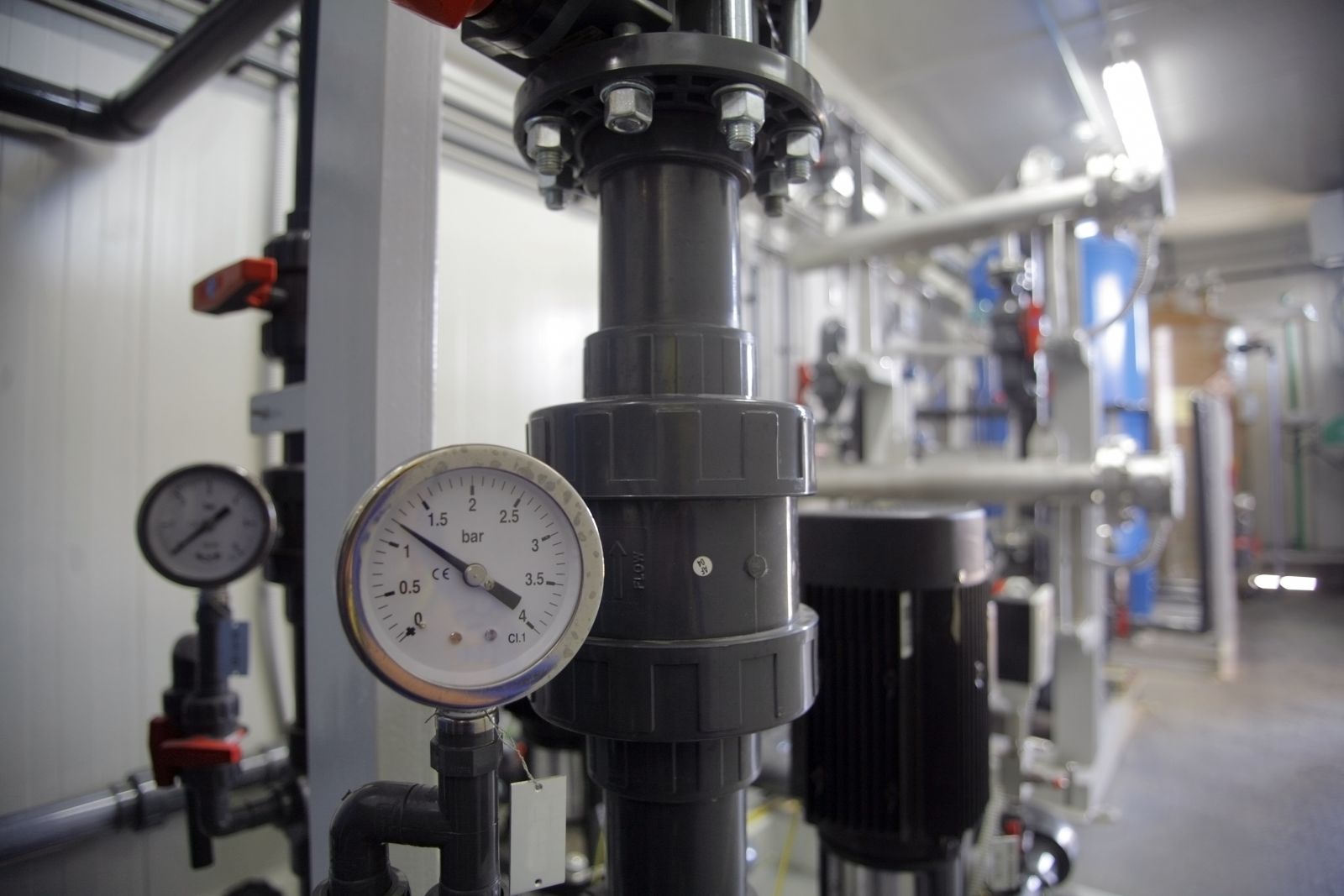
A detailed grasp of the particular industrial process, load analysis, steam pressure and temperature requirements, and safety considerations are necessary for determining the steam capacity for industrial boilers. A precise assessment of the steam capacity guarantees that the chosen boiler can consistently supply the necessary steam for the process while taking demand fluctuations and fluctuations into account. To effectively determine the steam capacity requirements and choose an appropriately sized boiler that is in line with both production needs and energy efficiency targets, collaboration between process engineers, boiler experts, and energy consultants is crucial.
Sizing and Space Requirements
In order to provide effective and secure operations across a variety of industries, industrial boiler sizing and space requirements are quite important. Calculating a boiler's proper capacity to meet the steam or heat requirements of a particular process while taking the installation area into account is known as boiler sizing. Here are some crucial considerations for industrial boiler sizing and space needs:
- Load Analysis and Sizing: The first stage in sizing an industrial boiler is a thorough load evaluation. This comprises calculating the amount of heat or steam needed for the process while accounting for peak demand, production fluctuations, and any planned expansions. The chosen boiler has to be able to meet process demands without working inefficiently or placing undue pressure on the equipment. A proper load analysis ensures this.
- Boiler Efficiency: For both maintaining energy efficiency and meeting production goals, selecting the right capacity boiler is essential. An undersized boiler could have trouble meeting peak demands, while an oversized boiler might waste energy while demand is low. For lower operational costs and a smaller environmental effect, the ideal capacity and efficiency mix must be found.
- Space Considerations: Industrial boilers come in a variety of sizes and configurations, which affects how much installation space is needed. The type of boiler, the fuel source, the combustion system, and any auxiliary equipment all have an impact on the installation's overall footprint. Ample space is needed for the boiler unit as well as for ideal ventilation, maintenance access, and adherence to safety regulations. To ensure that the chosen boiler can fit into the given area without compromising safety or operational efficiency, careful planning is necessary.
- Ventilation and Clearances: For safe combustion and heat exchange in industrial boilers, adequate ventilation is necessary. The area around the boiler must be kept clear enough to permit regular maintenance and repairs, as well as mechanical and natural ventilation. For the purpose of minimising overheating, reducing the possibility of accidents, and creating a healthy working environment for employees, compliance with local construction codes and safety requirements is crucial.
A rigorous procedure of load analysis, efficiency assessment, and space planning is required for industrial boiler sizing and space requirements. A boiler that is appropriately sized ensures that it can meet the heat or steam requirements of a certain process while yet being energy-efficient. It is also crucial to take into account the installation space that is available to support safe operations, adequate ventilation, and adherence to safety regulations. In order to accurately size and install boilers that match their production needs and existing infrastructure, industrial firms should consult with industry experts.
Materials and Durability
In the design and construction of industrial boilers, durability and material selection are important considerations. The materials used in a boiler's numerous components directly affect its performance, lifetime, and capacity to withstand challenging industrial process conditions. When it comes to industrial boiler materials and durability, keep the following in mind:
- Corrosion Resistance: In industrial boilers, extreme temperatures, pressure, and chemically adverse conditions typically occur. To avoid deterioration and increase the lifespan of the boiler, strong corrosion-resistance materials must be chosen. Stainless steels, nickel-based alloys, and other corrosion-resistant materials are frequently used for boiler components that come into contact with water, steam, and combustion fumes.
- High-Temperature Strength: For boiler applications, a material's ability to maintain structural integrity at high temperatures is crucial. In order to ensure the boiler's long-term durability, materials with high-temperature strength and creep resistance are chosen for the tubes, headers, and superheaters in boilers.
- Pressure Vessel Integrity: Industrial boilers operate at high pressure, therefore, pressure vessel materials must maintain their integrity. Pressure vessel materials must possess high tensile strength, toughness, and ductility in order to withstand the mechanical stress and pressure variations present during boiler operations.
- Weldability and Fabrication: A crucial process in the creation of boiler component parts is welding. The materials employed should be weldable in order to guarantee the production of solid and long-lasting weld connections. Additionally, it is important to take into account how the selected materials respond to different welding techniques and how they affect the boiler's overall structural integrity.
The choice of materials and their durability play a crucial role in the performance and longevity of industrial boilers. Corrosion resistance, high-temperature strength, pressure vessel integrity, and weldability are all significant variables to take into account when choosing materials for boiler components. The right materials help the boiler withstand the harsh conditions of industrial operations while also assuring safe and effective operation for the duration of the boiler's operating life. It's important to consult experts in materials engineering and adhere to industry requirements when choosing the materials for industrial boiler construction.
Fuel Options and Operating Costs
Operating costs, energy efficiency, and environmental concerns are all significantly impacted by the fuel choice for industrial boilers. These boilers can run on a variety of fuels, and deciding which is best relies on things like price, availability, pollution laws, and energy efficiency. Important considerations for industrial boilers' fuel options and running expenses are listed below:
- Fossil Fuels: Natural gas, oil, and coal are examples of conventional fossil fuels that have historically been used as boiler fuel in industrial settings. Because of its relatively low emissions, simplicity of combustion, and affordability, natural gas is frequently used. Less oil and coal being used because of increased emissions and volatile prices. The choice of fossil fuel is based on regional pricing and availability, adherence to emissions restrictions, and availability.
- Biomass and Biofuels: Alternatives to fossil fuels include biomass, which includes wood, agricultural waste, and crops grown specifically for energy, as well as biofuels like biodiesel and ethanol. These choices are appealing due to their less negative effects on the environment and ability to minimise greenhouse gas emissions. Regional sourcing of biomass and biofuels can boost local economies and lessen reliance on imported fossil fuels.
- Electricity: Electric boilers are a clean and effective solution because electricity is their primary energy source for heating. Although the cost of electricity per unit of energy can be higher than that of some fossil fuels, electric boilers offer better rates of energy conversion and require less upkeep. The availability and cost of power in a particular area are frequently factors in the decision to use electricity as a fuel.
- Operating Costs: The cost of running industrial boilers is directly impacted by the fuel choice. The overall cost of running a boiler is affected by elements like fuel cost, combustion efficiency, and maintenance needs. Even though some fuels may be less expensive initially, they may have greater operational costs in the long run because of inefficiencies or increased emissions. The original investment and ongoing operational costs should both be taken into account in a thorough cost analysis.
For industrial boilers, choosing the best fuel option is a crucial choice that has an impact on operational costs, environmental performance, and energy efficiency. Electricity, biomass, biofuels, and fossil fuels all have their own benefits and drawbacks. To choose the best fuel alternative for their industrial processes, businesses must consider variables such as fuel supply, cost, emissions standards, and long-term sustainability. Making well-informed judgements that are in line with both financial and environmental objectives can be facilitated by working with energy specialists and performing detailed cost studies.
Compliance and Safety Regulations
It is critical to ensure that boiler goods in Australia comply with all regulations. Different organisations establish safety standards and procedures to ensure that boilers operate properly and safely. The following are some of the most important boiler supply regulations in Australia:
- AS/NZS 1200: Australian/New Zealand Standard for pressure equipment, covering design, construction, and operation of boilers.
- AS 4343: Australian Standard for pressure equipment made from wrought and cast steels, ensuring material compliance and integrity.
- Work Health and Safety (WHS) Regulations: Govern occupational health and safety, including boiler installation, maintenance, and operation.
Ensuring Compliance with Safety Standards and Certifications
When selecting boiler equipment, it is critical to prioritise safety, and achieving safety requirements and certifications is a key part of that. In Australia, seek for the following safety rules and certifications:
- AS 3873: Australian Standard for pressure equipment - Operation and maintenance.
- AS 61508/AS 61511: Standards for functional safety of electrical and electronic systems for process industries, including boiler safety controls.
- ISO 45001: Certification for occupational health and safety management systems, ensuring a commitment to safe practices.
Considering Safety Features and Maintenance Requirements
Safety features are critical for ensuring that stoves operate safely. When purchasing boiler supplies, consider for key safety features such as:
- Pressure Relief Valve: Safely releases excess pressure to prevent boiler explosions.
- Flame Failure Device: Automatically shuts off the fuel supply if the flame goes out, preventing gas leaks.
- Low Water Cut-off: Shuts down the boiler if the water level drops too low, protecting against dry-firing.
Boilers in Australia must be tested and serviced on a regular basis to ensure that they operate safely and efficiently. Hire competent experts to do regular inspections and maintenance, as well as to identify and resolve any potential safety issues as soon as feasible.
It is critical to understand and follow regulatory criteria when selecting boiler supplies in Australia to ensure that safety standards and certifications are satisfied. Boilers operate more efficiently and safely when safety measures are prioritised and maintenance requirements are met. Businesses and residences in Australia may ensure that their heating systems will perform well and dependably while keeping people safe and healthy by selecting boiler supplies that adhere to the standards and are safe.
Maintenance and Support
The reliable and effective operation of industrial boilers over the course of their operating lives depends on maintenance and support. Reduced downtime, increased boiler longevity, and worker safety are all benefits of routine maintenance, prompt repairs, and availability to technical support. Key considerations for industrial boiler maintenance and support include the following:
Scheduled Maintenance: For industrial boilers to operate at their best and avoid unexpected breakdowns, routine maintenance must be performed on a regular basis. Cleaning, inspecting, and calibrating various components, such as burners, heat exchangers, valves, and safety devices, are all maintenance jobs. Potential problems can be found and resolved by sticking to a clearly laid out maintenance programme before they develop into expensive failures.
- Emergency Repairs: Unexpected problems can happen despite careful upkeep. It's critical to respond to emergency repairs quickly in order to reduce production downtime and associated safety risks. In order to immediately resume regular operations, boiler operators should have access to qualified experts who can quickly diagnose issues and carry out efficient repairs.
- Technical Support: For addressing operational concerns, diagnosing problems, and guaranteeing the correct operation of industrial boilers, access to qualified technical support is essential. Boiler operators can receive professional advice from manufacturers and service providers, who can guide them in making decisions and putting best practices into practice to preserve efficiency and safety.
- Training and Education: For industrial boilers to operate safely and effectively, properly trained employees are required. Numerous topics, including boiler operation, maintenance techniques, safety regulations, and emergency response, can be included in training programmes. Operators who have received proper training are better able to see possible problems, perform routine maintenance, and handle crises.
The efficient operation of industrial boilers depends on maintenance and support. Boiler performance is safe and effective when it is supported by routine maintenance, prompt repairs, technical assistance, and training programmes. Businesses can increase the lifespan of their boilers, maximise operating efficiency, and protect the safety of both workers and the surrounding environment by adhering to routine maintenance schedules, attending to emergency repairs quickly, and assuring access to professional counsel.
Future Technological Advancements
Significant technology breakthroughs that promise improved operational control, decreased environmental impact, and better efficiency are on the horizon for industrial boilers. Researchers and engineers are investigating novel strategies to enhance the design, composition, and efficiency of industrial boilers as businesses continue to place a high priority on sustainability and energy efficiency. Important things to think about with reference to industrial boilers' prospective technical development are listed below:
- Digitalization and Automation: Industrial boiler operation and maintenance will change as a result of the integration of digital technologies like IoT (Internet of Things) sensors, enhanced data analytics, and automated systems. These innovations enable the optimisation of fuel usage, predictive maintenance, and real-time monitoring of boiler operation. Operators can minimise operational costs, prevent downtime, and improve energy efficiency by using data to drive their decisions.
- High-Efficiency Combustion: The goal of advanced combustion technology research is to improve industrial boilers' combustion efficiency. Higher thermal efficiency and reduced emissions are possible with the help of technologies like chemical looping and oxy-fuel combustion. These developments increase energy conversion rates while simultaneously lowering greenhouse gas emissions and helping to comply with more stringent environmental requirements.
- Carbon Capture and Utilisation: Carbon capture and utilisation (CCU) technologies are being investigated in the context of industrial boilers as industries strive to become carbon neutral. With the help of these technologies, carbon dioxide emissions from combustion can be captured and turned into useful items like chemicals or construction materials. Industry might minimise its carbon footprint while generating more value from waste streams by implementing CCU in industrial boilers.
- Hybrid Systems and Renewable Integration: Industrial boiler energy efficiency could be improved by hybrid systems that mix conventional fossil fuels with renewable energy sources like solar thermal or biomass. Industries can lessen their reliance on fossil fuels and their environmental impact by incorporating renewable energy into the boiler's heat-producing process. These hybrid systems might also give businesses more operational flexibility, enabling them to adjust to changing energy availability and demand.
Technological developments that embrace digitization, improve combustion efficiency, support carbon capture and utilisation, and incorporate renewable energy sources will define the future of industrial boilers. The increased demand for environmentally friendly and energy-efficient products across industries is what's driving these advances. The industrial sector may look forward to a new era of boilers that offer higher performance, decreased emissions, and greater adaptability to shifting energy landscapes as research and development activities continue.
In Conclusion
In conclusion, it is critical to make informed decisions about the suitable industrial boiler supplies if you want to increase the performance of your business. Numerous factors, including load analysis, fuel options, maintenance, and the use of technology, influence efficiency and sustainability. We firmly advise businesses to conduct in-depth research, consult industry experts, and carefully weigh all of their options. By doing this, companies may link their decisions to operational needs, contribute to a greener future, and save costs, all of which will assure their long-term success in the industrial sector's continually evolving environment.